Quality differentiation by controlling leakages of your packages
Why measuring leak rate at known pressure conditions is the best way to make a differentiation in the quality of your packaging process and helps you at any step of realization and decision?
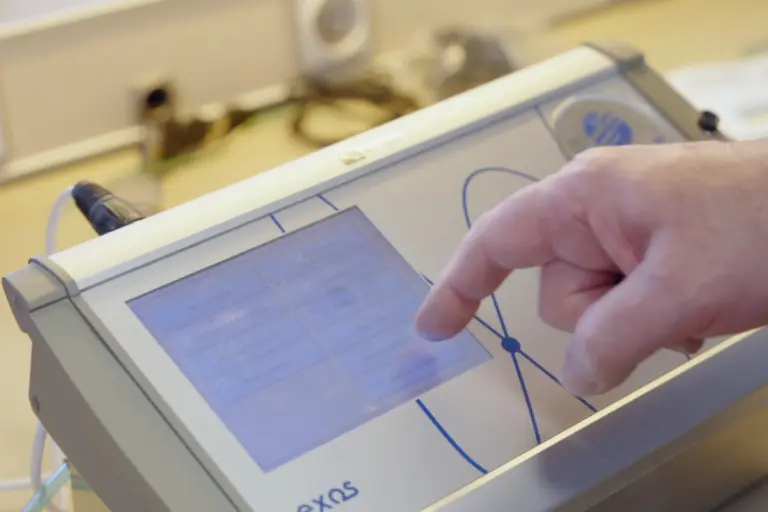
Packaging leak measurement is a top priority subject because leak measurement improves the shelf life of the product. Today it has become a crucial means to be cost-effective by optimizing the quantity of matter (size, thickness and type of foil) or by speeding the setup of the machinery (heat, time of seal). Keeping flavors and taste is a must-have to give full satisfaction of the consumer.
For instance, salted biscuits and snacking companies are worried about the crispiness of the product, which is damaged very fast in the presence of humidity or O2 uptake, particularly if the packaging is punctured. Defects of the envelope and sealings can easily annihilate the barrier property of the film and for gas flushed packs increase expenses to keep the O2 level low (increase of gas consumption, headspace, lower initial rate, scavengers, more complex films …).
Moving from location testing method to measuring instruments
Good manufacturing practices in dry food production forbids the use of water in area of production mainly because of hygiene practice and direct negative effects on product by generating a source of humidity in the production area. Consequently, leak measurement by using an air-air testing method is more relevant than leak detection using a water bath (Bubble Leak Test based on ASTM F 2096, or DIN 55508-1).
Having a view of the location of a defect is not a true reflection of the exchange rate of the inner atmosphere or representative of real-life conditions. Having bubble emission naturally expressed without stress conditions is simply not possible. The stress generated on the package is often done with uncontrolled pressure difference that can result in a burst inside the water bath rather than revealing weaknesses in the packaging process.
A new challenge is the move to a more paper-based solution in the packaging industry. The water bath method will immediately destroy these packages, so an air-to-air technique is the only answer.
Transportation method and conditions can also affect the exchange rate of the internal atmosphere through the defects of the package
The variations of pressure occurring because of altitude, meteorologic, and temperature changes can be generated at different speeds in regards of the transportation means and destinations. Therefore, the evaluation of exchange rates between the inner and outer atmosphere, cannot only be limited to use permeation property of the film but is effectively a result of massive diffusion through the open area of the defects.
Simply because defects generated by the process of packaging give a much higher diffusion rate through the surface of defects, in a proportion which is drastically compromising the initial calculated permeation rate.
But because having the result of the defect by waiting for the equilibrium of molecules is a relatively long process, measuring the quantity of air escaping from the inner volume gives a quicker, more consistent and trustful valued result.
At the same time, having a too high air fill (which in addition could increase the internal pressure) and airtight package can both contribute to a burst with altitude or quick pressure changes (storms can generate a sudden drop of 50 mbar pressure in a day for instance, and take off 200 mbar down pressure in 20 min).
Because of this stress exerted just after the last sealing all along the conveyors and logistics chain, it is important to have a metrological leak test to determine the appropriate means to preserve the inner atmosphere.
Effects of defects vs permeation of film
As an example, in snacking flow pack flushed with N2:
A defect of structure on a 10 × 10 × 1 cm packaging (100 mL headspace volume) made from a 100 µm thick plastic film seen as a straight pinhole of 100 µm diameter dramatically increases the rate of O2 uptake:
- 10 times faster than permeation through a single PE film
- 10 000 – 100 000 times faster than permeation through a single EVOH film
(with a film surface/pinhole area ratio ≈ 5 × 106)
And for water vapor, it is worse: the diffusion rate of water vapor in air is 2 times quicker than O2.
Reference method for leak measurement
In many techniques of leak detection and measurement, some variables are still unknown to determine the relevant exchange rate. Essentially because both internal pressure and volume of headspace during the test are not known to get the correct estimation of leak rate.
Therefore DIN55508-1 was published and describes a technique of leak by measuring the flow rate at constant pressure. This makes the test consistent, sensitive, and versatile for any kind of packages and solid contents.
How leak measurement helps your pilot
With the complexity of realization, having DIN55508-1 based instruments such as Exos or Oxylos, makes the life of the packaging engineer easier to have minimal variables of influence, high sensitivity, and controlled pressure conditions with any form and construction of the packaging is.
The Exos solution is quite versatile, easy to use, and can provide KPI to supervise the quality of the production line. The Exos applies a preset test pressure, then calculates the amount of flow required to maintain that pressure. The flow is an aggregate of all leaks through the package while other techniques provide no data at all.
Then you can easily look at the distribution of values and deviation of the quality of the seal as shown on the next figure:
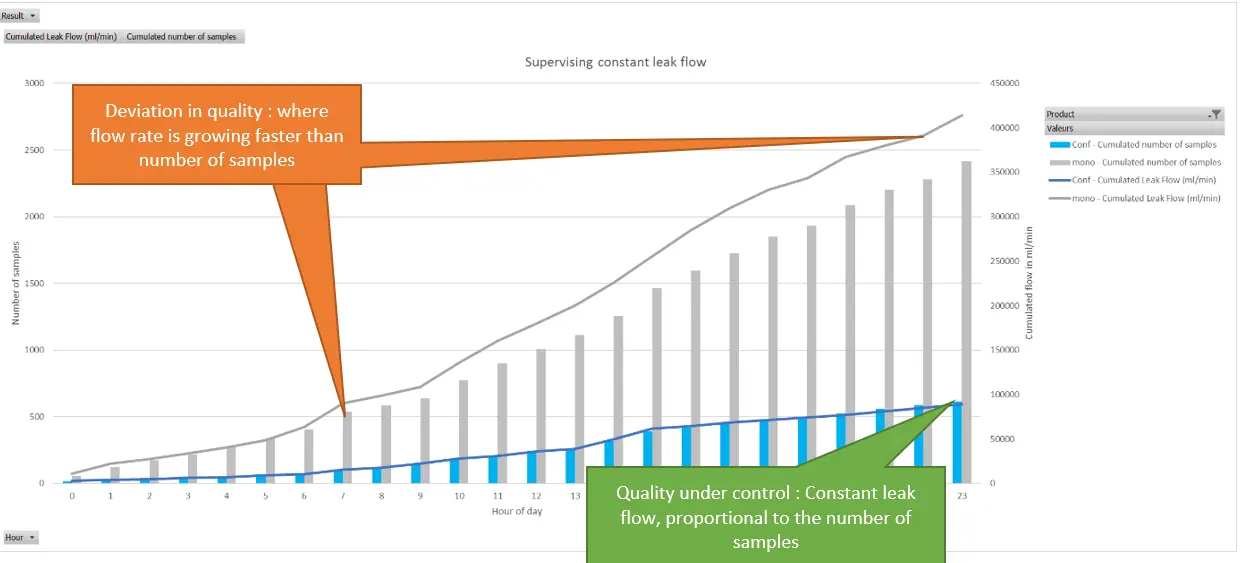
Additional features for MAP application
Moreover, Exos and Oxylos can have gas analysis to be measured in addition to the leak measurement, which helps in knowing the initial atmosphere of the package and helps to anticipate the effect of leak size against gas changes by directly correlating both values.
Benefits and rewards for the food industry
DECISION HELPER
The sensitivity of the device allows to discriminate by experiment, the causes of leak among the following examples:
• The perforation of the film
• The best matter for the film vs leak level
• The quality of the sealing
• The presence of product in the seals
• The effect of settings on machinery in the performance
• The phenomena of tiredness (creep test)
Commit to trustful specifications
The technique used by Exos® and Oxylos® allows to control complying DIN 55508-1 standard:
• Strength of the sealing
• Leak measurement (down to 5µm)
• Breathability of the packaging
• The uptake of gas over time for modified atmosphere applications
The reached performances are such as the sensibilities, or detection limit, can go down to 5µm equivalent diameter perforation at low stress.
This is at this condition of effective sensitivity that packaging solutions can be truly evaluated. This instrumentation gives the right tool to measure and track improvements to finally act for the most cost-effective solution and becomes a true asset of differentiation by quality to develop your strategic markets.
Make food safer
Knowing the modified atmosphere without leak measurement could expose to a wrong conclusion in case a contamination is detected in a package while gas level is still seen good after few hours.
Even if a 0.5 to 2µm sized pathogen has no legs to pass through a 5µm puncture, an initial population of E.Coli within the pack could be multiplied by 10 in 50 hours if a certain mass of O2 is supplied through the defects of structure. For instance, after 15 hours, the headspace can still be measured below 1% O2, but with a defect as low as 1ml/min leak rate and kept 6 hours in a condition of only 10 mbar pressure difference, brings the require number of molecules to make the pathogen grow.